Wood chips pallet blocks are an essential component of pallet manufacturing. They provide sturdy and durable support for various industries, including logistics, warehousing, and packaging. In this article, we will explore the Wood Chips block machine and the entire wood chips pallet block production process.
1. Choose the right block machine
At PalletsBiz, we offer three pallet block machines tailored for small to medium-sized pallet factories:
1. Single Head Pallet Block Machine
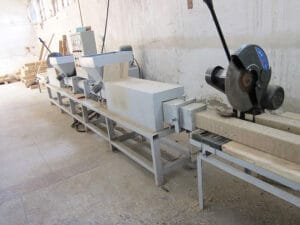
A single heads block machine is a compact and efficient wood pallet block production machine featuring one outlet per end. It is ideal for small to medium-scale production and allows manufacturers to produce compressed pallet blocks with minimal waste while maintaining high-quality standards.
2. Double Heads Pallet Block Machine

The double heads block machine, also known as a dual-outlet pallet block machine or compressed wood block-making machine, is designed for efficient and high-volume production of wood pallet blocks. This machine is ideal for recycling wood waste into durable and uniform pallet feet (pallet legs) used in compressed wood pallets.
3. Triple Heads Euro Pallet Block Machine
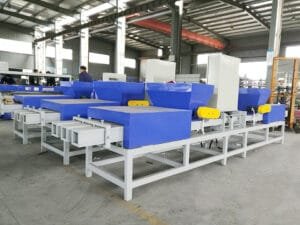
The three heads block machine, also known as a triple-outlet wood pallet block machine or compressed sawdust pallet block press machine, is designed for high-speed and high-volume production of wood pallet blocks. This machine efficiently recycles wood waste, such as sawdust, wood chips, and shavings, into strong, uniform pallet blocks, making it a cost-effective and eco-friendly solution for the pallet industry.
Their key differences lie in output capacity and block size compatibility. All models support standard Euro pallet blocks. For custom sizes or shapes, contact us today for expert assistance!
2. Define Your Wood Pallet Production Needs
Two important factors need to be considered:
1. Block Size

The standard specifications for Euro pallet blocks are as follows:
100 mm x 145 mm x 78 mm
145 mm x 145 mm x 78 mm
Also some special sizes like :
160 mm x 95 mm x 95 mm
95 mm x 95 mm x 95 mm
145 mm x 145 mm x 78 mm
145 mm x 100 mm x 78 mm
78 mm x 78 mm x 78 mm
…
2. Production Quantity
How much demand is there for each block specification? This determines how to allocate the number of pallet block machines.
3. How are woodchip blocks for Euro pallets produced?

1. Raw Material Collection
The production of wood chips pallet blocks starts with collecting waste wood, sawdust, wood shavings, and wood chips from sawmills and furniture factories. These eco-friendly pallet blocks help reduce deforestation by recycling wood waste. Contaminants like nails and plastics are removed to ensure high-quality compressed pallet blocks.
2. Crushing & Grinding
Workers process the sorted wood materials first. Through a wood crusher or hammer mill to creates uniform wood chips or fine sawdust. The chip’s size is essential for durable presswood pallet blocks. This step ensures consistency in the final pallet block production.
3. Drying Process
To achieve the optimal moisture content of 8-12%, the wood chips are dried using rotary drum dryers or belt dryers. Proper drying enhances the bonding strength of molded pallet blocks and prevents cracking or deformation, making them ideal for pressed pallet manufacturing.
4. Adhesive Mixing
Workers mix dried wood particles with industrial adhesives, such as Urea – Formaldehyde (UF), Melamine – Urea – Formaldehyde (MUF), or Methylene Diphenyl Diisocyanate (MDI). These adhesives enhance durability and water resistance, ensuring the longevity of compressed wood pallet blocks.
5. Compression Molding
The adhesive-mixed wood chips are placed in a hydraulic pallet block extrusion machine. The mixture is compressed under high pressure and temperatures of 150-200°C. This process creates high-strength pressed wood pallet blocks suitable for logistics and export packaging.
6. Cooling & Cutting
After molding, workers cool the hot compressed pallet blocks to maintain their shape and structural integrity. Once cooled, they cut the blocks into standard pallet block sizes, such as 90×90 mm, 100×100 mm, and 145×145 mm, as required for various wood pallet applications.
7. Quality Inspection
Each batch of presswood pallet blocks undergoes strict quality inspections. The inspection includes moisture analysis, density measurement, compression strength testing, and durability checks. Blocks that do not meet industry standards for pallet manufacturing are reprocessed to maintain high-quality control.
8. Packaging & Storage
Workers bundle the finished compressed pallet blocks, wrap them in plastic film, and store them in dry, ventilated warehouses to prevent moisture absorption and ensure long-term durability. Proper storage conditions maintain the integrity of wood pallet blocks for shipping and distribution.
9. Delivery & Application
Manufacturers supply the final wood chips pallet blocks to pallet producers, providing a sustainable and cost-effective alternative to solid wood blocks. Logistics, warehousing, and global exporters widely use these eco-friendly pallet blocks because of their strength, uniformity, and pest resistance.
Why Choose Presswood Pallet Blocks?
✅ Eco-friendly & Sustainable – Made from recycled wood waste, reducing deforestation.
✅ High Strength & Durability – Ideal for compressed pallet block production.
✅ Cost-effective & Customizable – Available in various pallet block sizes and specifications.
By following this efficient pallet block production process, manufacturers transform wood waste into high-quality pallet blocks. it supports sustainable development and a circular economy in pallet manufacturing.