The production of Presswood pallets involves several steps that can release harmful gases, particularly during the bonding and curing processes. For manufacturers, it’s crucial to implement proper safety measures to ensure both the quality of the product and the health of the workers. In this article, we’ll explore practical strategies to minimize the risk of harmful gases, ensuring a safer working environment.
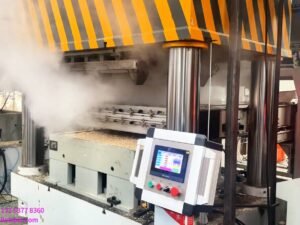
1. Choose Safe Adhesives for Presswood Pallet Manufacturing
One of the key sources of harmful gases in presswood pallet production is the glue used for bonding. Urea Formaldehyde (UF) resin, commonly used in the past, can release formaldehyde gas, a known carcinogen that poses serious health risks to workers.
To minimize exposure, it’s recommended to:
- Avoid UF adhesives: If UF resin must be used, ensure it is of E0 or E1 grade, which have lower formaldehyde emissions. However, these still release some harmful fumes.
- Use MDI (Methylene Diphenyl Diisocyanate) adhesives: MDI is a much safer alternative, releasing fewer toxic substances and improving air quality in the workshop. It’s specifically formulated for presswood pallet production, making it the ideal choice for reducing harmful emissions during the manufacturing process.
Switching to MDI adhesives not only ensures a safer working environment but also contributes to environmental protection by reducing pollution levels.
2. Ensure Proper Ventilation and Airflow
A well-ventilated workshop is crucial for reducing exposure to harmful gases. Stale air can trap fumes and increase their concentration, putting workers at risk.
- Maximize airflow: Workspaces should be spacious enough to allow for free movement of air, preventing the buildup of toxic fumes.
- Install exhaust fans: Ensure the installation of high-efficiency exhaust fans to expel fumes generated during production, particularly around the pressing machines and mold areas.
- Maintain continuous ventilation: It’s important to keep air circulation constant, as harmful gases may build up even in moments of low activity.
Good airflow can significantly reduce the concentration of airborne toxins and improve overall air quality in the production area.
3. Use Negative Pressure Extraction Systems
Installing a negative pressure extraction system near the Presswood machines and press areas is a highly effective way to control harmful gas emissions.
- Place exhaust units above presses: This system draws harmful gases from the production area, capturing them at their source before they can spread into the wider workshop.
- Filtration and purification: After extracting the gases, it’s essential to use filtration systems to clean the air before releasing it back into the environment. High-efficiency particulate air (HEPA) filters or activated carbon filters can effectively remove toxic particles from the air.
This method is especially useful for keeping the air clean in areas where presswood pallets are being formed under high heat and pressure.
4. Personal Protective Equipment (PPE)
In addition to improving the work environment, personal protective equipment (PPE) plays a critical role in reducing exposure to harmful chemicals.
- Wear dust masks with filtration capabilities: Dust masks equipped with filters designed to capture fine particles, fumes, and gases should be worn at all times in the workshop.
- Wear appropriate work clothing: Protective gloves, safety goggles, and work uniforms help shield workers from exposure to harmful chemicals that may come into contact with skin.
- Ensure regular PPE maintenance: PPE should be inspected regularly and replaced when worn out or damaged to ensure its effectiveness.
Properly maintained PPE ensures that even if ventilation systems fail, workers are still protected from inhaling harmful substances.
5. Routine Safety Training and Monitoring
In addition to physical safety measures, it’s essential to regularly train workers on the importance of health and safety practices.
- Safety protocols: Provide ongoing training on handling materials safely and following safety procedures during production.
- Monitor air quality: Use air quality monitoring systems to regularly check for any increase in toxic gases in the workshop.
This approach not only promotes a safer working environment but also fosters a culture of safety and responsibility in the workplace.
Conclusion
Ensuring the health and safety of workers in the presswood pallet production industry is critical. By choosing safer adhesives, improving ventilation, installing extraction systems, using proper PPE, and implementing regular safety training, manufacturers can significantly reduce the risks associated with harmful gases. Protecting workers not only complies with safety regulations but also improves the overall efficiency and sustainability of the production process.
If you need help implementing these safety measures or learning more about presswood pallet production, feel free to reach out to us at PalletsBiz, a leading presswood pallet machine manufacturer. We are committed to providing high-quality, environmentally friendly solutions for the pallet industry.